UTokyo researchers answer questions on 21 GX (Green Transformation) topics from their specialist viewpoints. Through questions that cannot simply be brushed off as someone else’s concerns, take a peek into GX and our world of research.
Q19. Can buildings really be constructed with leftover Chinese cabbage?
Some researchers are creating new materials out of food waste! Are they really trying to make houses out of vegetables?Answered by Yuya Sakai
Associate Professor, Institute of Industrial Science
Sustainable Construction Materials Engineering
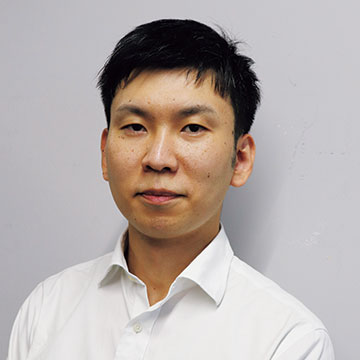
It started out as research into concrete recycling
Concrete is made by mixing water and cement with sand and gravel. The cement, which consists mainly of limestone, fills the gaps between the sand and gravel and functions as an adhesive. Second only to water, the global usage of concrete is more than double that of iron, wood and plastic combined. This results in the generation of huge amounts of rubble, with few options for recycling other than crushing it for use as a road filler. Moreover, the production of cement accounts for 8% of total global carbon dioxide emissions. With these circumstances in mind, we have been looking into the recycling of concrete for the past six years.
While investigating the mechanism by which moisture causes concrete to contract and expand, we discovered it was possible to compact pulverized rubble into materials that were stronger than the original concrete. Although initially unsuccessful, we were able to increase the strength to unexpectedly high levels by adjusting the powder size, applying high-pressure steam treatment hardening, and forcing the materials to absorb carbon dioxide. We think that this process caused the calcium hydroxide to turn into calcium carbonate, which then filled the gaps between the sand and gravel.
Next, we wondered if something like wood could be used as an adhesive in place of the cement. By mixing equal amounts of wood waste powder and concrete rubble and compacting the mixture while hot, we were able to produce a potentially biodegradable botanical concrete, with the lignin in the wood acting as an adhesive. Then, as an extension of that, we tried exchanging the wood powder with other materials. Tea leaves, for example, resulted in a material with a nice fragrance. Finally, inspired by our visions of dried gourd kneaded into the walls of Kumamoto Castle to prepare for a possible besiegement, we started to consider using edible ingredients in the form of waste materials from fruits and vegetables. Whether it consists of the non-edible parts or nonstandard produce, a lot of fruit and vegetable material is thrown away, so we wanted to make use of it.
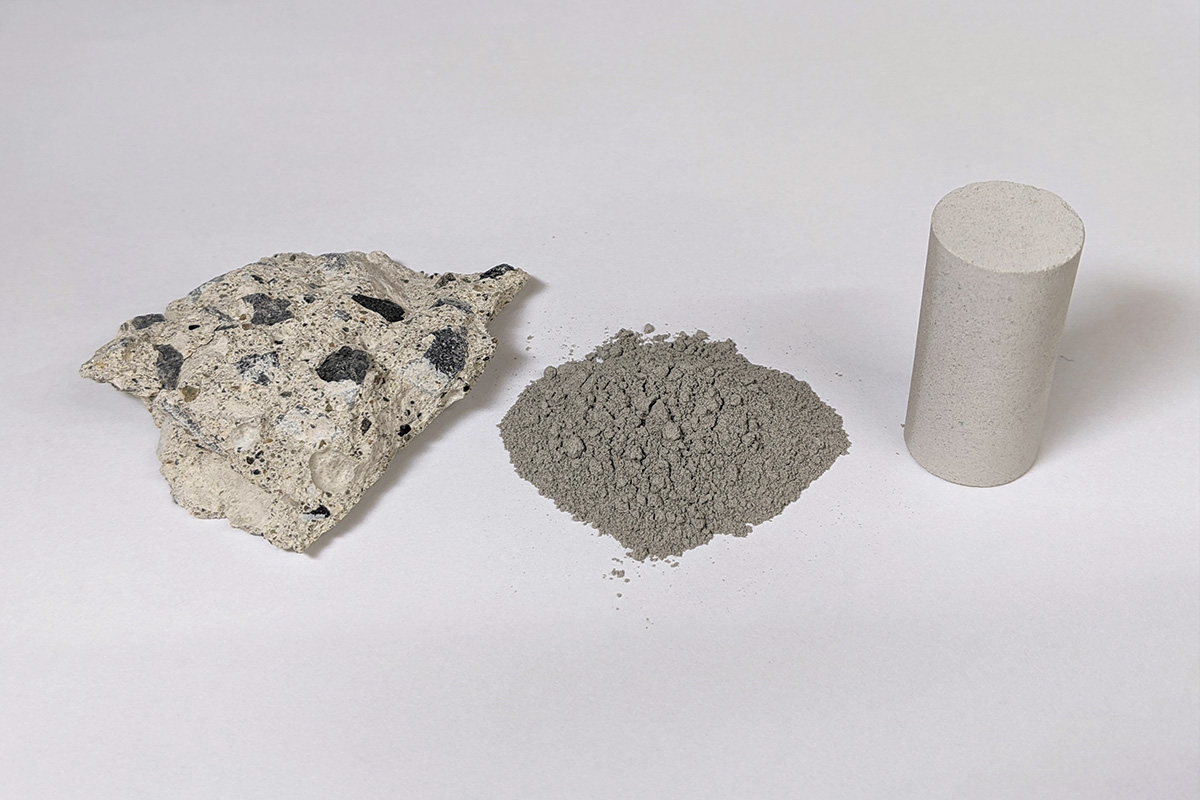
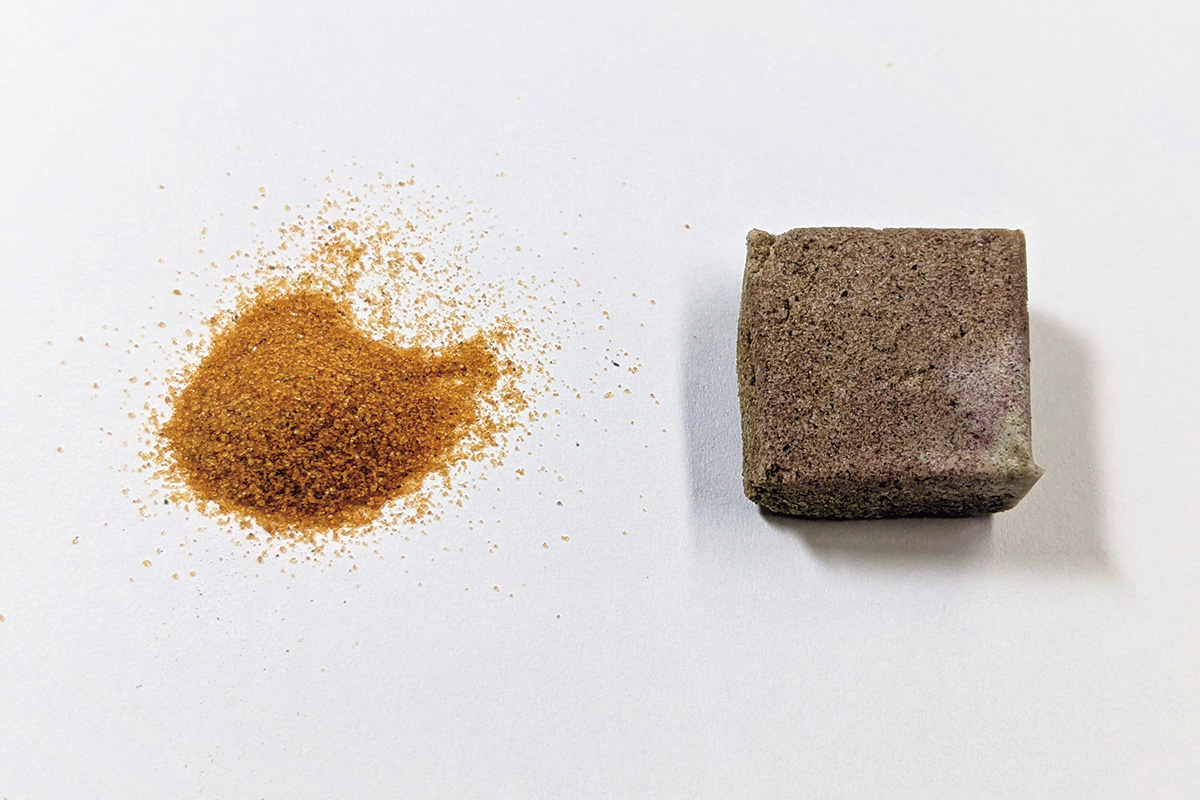
Using Chinese cabbage to make a material quadruple the strength of concrete
Materials with sufficient strength for use as building materials were obtained from 30 types of waste foodstuffs, such as cabbage and orange peel. After first drying and pulverizing the waste, water was added, and the mixture was compaction molded while being heated. We had expected in advance that kabocha skin and burdock root would make strong materials, but Chinese cabbage turned out to be the strongest with a bending (flexural) strength of 18 MPa, four times higher than regular concrete. Even when the same food material is used, the strength varies according to powder size, processing temperature or even the drying method. The way in which the sugar content and dietary fiber are combined also seems to have an influence. When heated, the sugar (glucose) in the fruits and vegetables softens, flows into the gaps and sticks there. However, this does not mean that materials get stronger as their sugar content increases. Mutual interactions between the sugar and dietary fiber yield stronger materials than those containing only one or the other of these components. Chinese cabbage seems to contain a perfect balance of sugar and fiber.
Other advantages of using food waste ingredients are that they provide fragrance and color, and might also be edible. The manufacture of goods based on local specialties is also a promising market, with examples including coasters made with mandarin orange peels from Ehime Prefecture and plates made with coffee grounds from Costa Rica. Although materials based on a mixture of plastic and waste foodstuffs already exist, we think that those based 100% on food waste are new. As is the case for freeze-dried goods, food-based materials can be sensitive to moisture, but a startup founded by one of our former students who wrote his graduation thesis on this subject is offering urethane-coated products with improved water resistance.
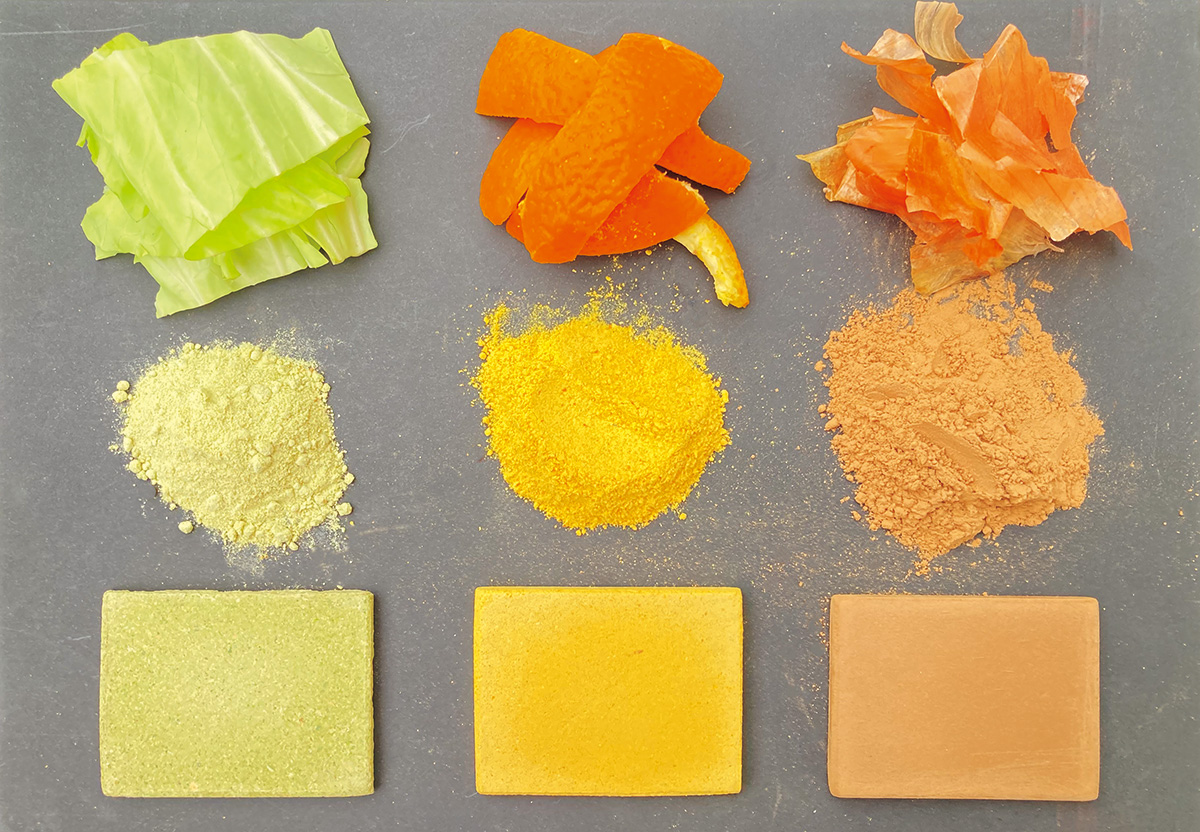
Converting disaster zone rubble, desert sand and moondust into building materials
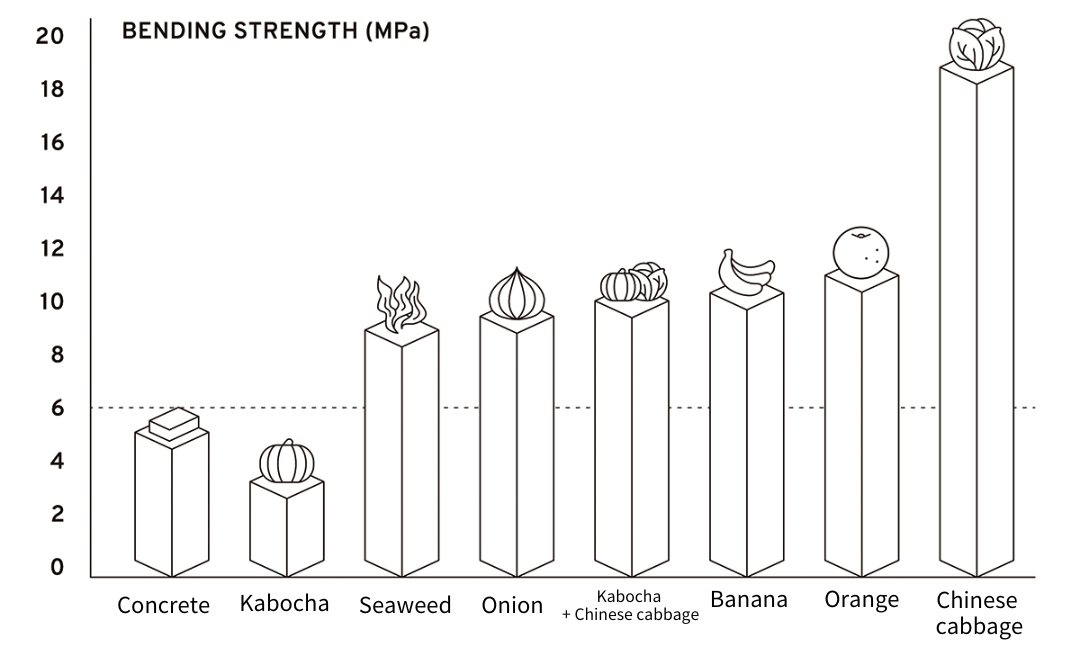
All that is needed to produce our recycled concrete are a pulverizer and a pressing machine. If just these two items are loaded onto a truck and taken to a disaster zone, the rubble lying there can be converted into building materials. We then don’t need to carve out mountains to excavate materials for new cement, and the CO2 emissions will be about one third of those from the regular process. We have already exposed such recycled concrete to the rain for around to two to three years and seen no major changes to its durability. Considering such results, we are now conducting joint research with a private company, starting with the development of concrete blocks.
Suitable grades of sand and gravel are currently in short supply. Desert sand, for instance, is ordinarily too fine to use in concrete, but we have developed a technology whereby a heated mixture of sand, ethanol and an alkali metal catalyst will harden overnight. This process repeatedly breaks and reforms the chemical bonds in the sand, getting the grains to stick together to produce concrete blocks from the previously unusable desert sand. Just by using a cheap catalyst such as potassium hydroxide and heating to 110°C, we can achieve a material with similar strength to concrete, and we are now working with a company to research how to commercialize this process. Perhaps in the future we might even be able to make building materials for bases on the Moon from locally sourced moondust.
My startup business revitalizing food waste
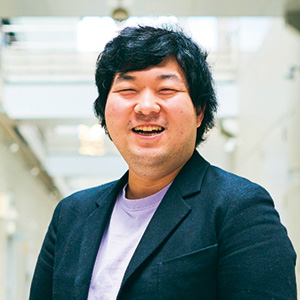
CEO, fabula Inc.
In June 2020, Associate Professor Sakai suggested I study materials made from food waste for my graduation thesis. After returning from Costco with a huge amount of fruit and vegetables and doing lots of experiments with them, I submitted my thesis in February 2021. After graduation, thinking it would be nice to utilize the results of my research in society one day, I had a chat with a couple of old friends from my primary school days, and in October 2021 the three of us started fabula.
- Company logo reflecting the basic components for various products
https://fabulajp.com
We receive many orders for novelty items like keychains and magnets that are used as sales promotion goods at exhibitions. As well as starting a new collaboration with a lacquerware manufacturer, we are planning to provide the architects in charge of the galleries at Expo 2025 Osaka with our technology for making food waste into building materials.
While naturally we want people to recognize the value of transforming unwanted trash into something new, I think we must also make them feel that our products are genuinely good.